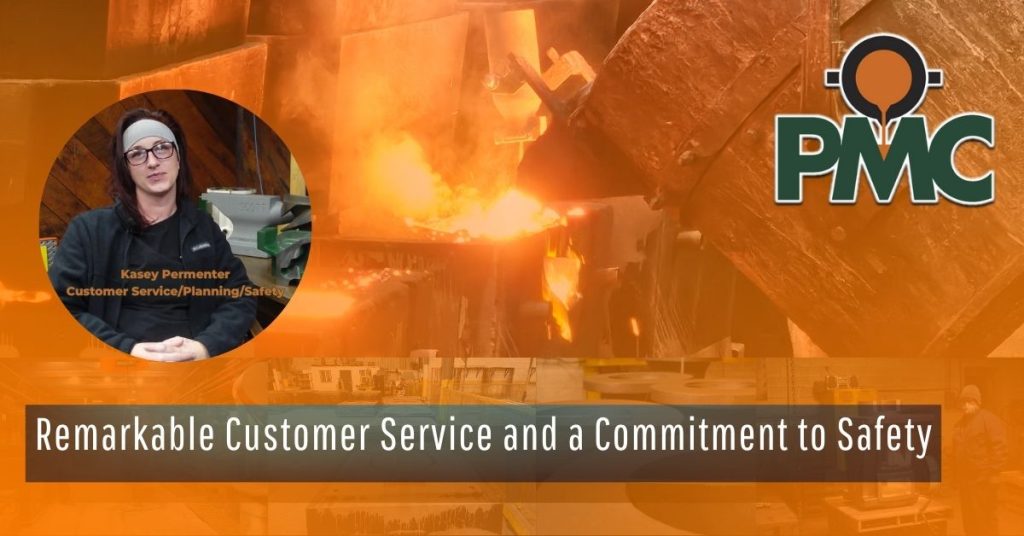
At Penn-Mar Castings, our team is committed to making your customer service experience the best it can be.
Our staff is dedicated to putting your needs first and getting your parts out the door in a timely fashion.
“I make it a personal goal to make sure I have a response within two hours to our customers,” said PMC customer service/purchasing/safety coordinator Kasey Permenter. She went on to say PMC honors requests to expedite, as they usually have a very, very low lead time. “We try to provide as much as we can for our customers, depending what they ask, we go above and beyond.”
Striving for constant quality improvement
Penn-Mar Castings is committed to improving quality management through the use of education, innovation and quality tools. That improvement means both internal and external communication.
PMC often schedules customer visits to solve any quality issues in a timely manner. This effort to continuously improve includes increasing manufacturing efficiencies, improving process control, expanding capabilities and updating facilities.
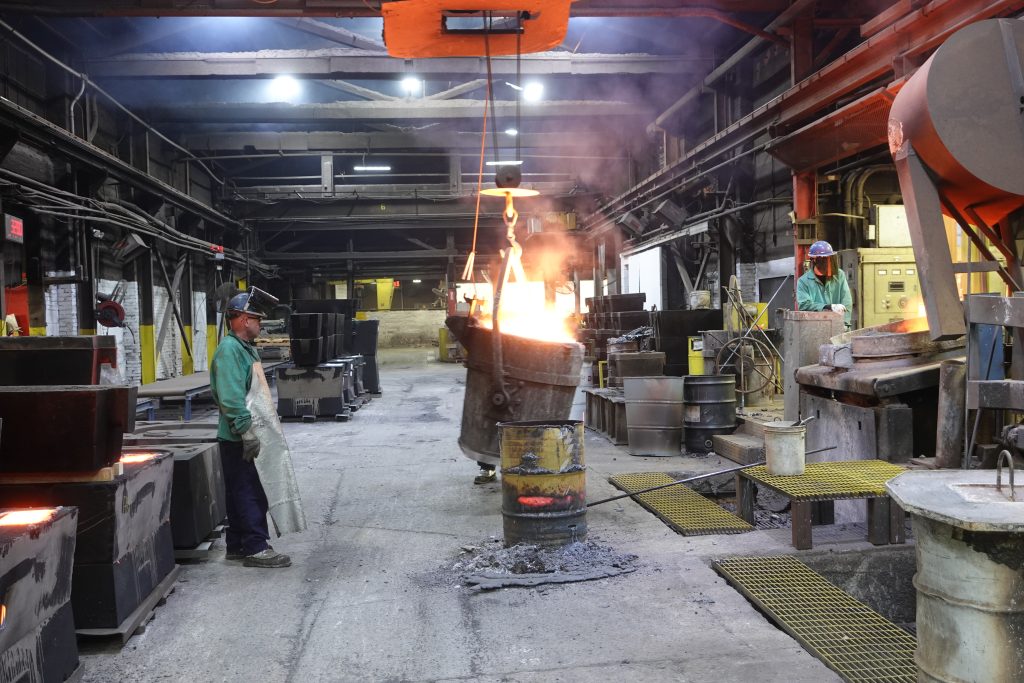
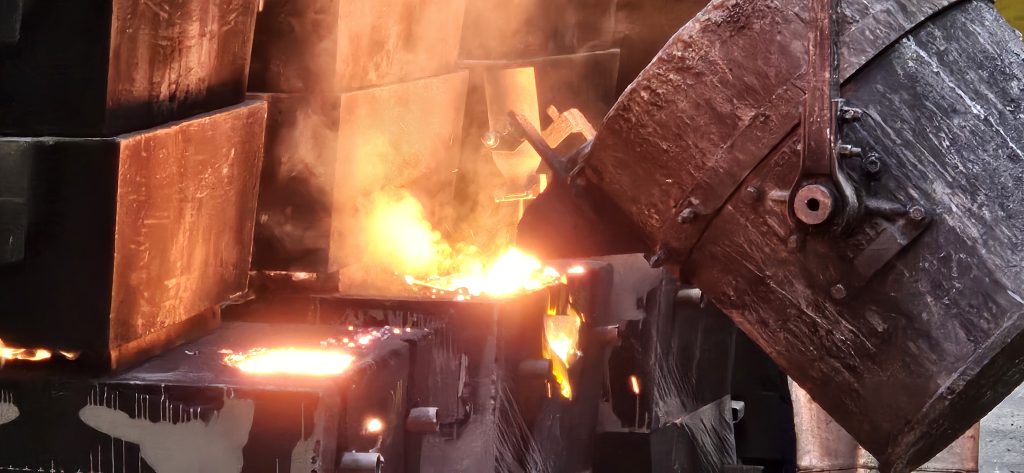
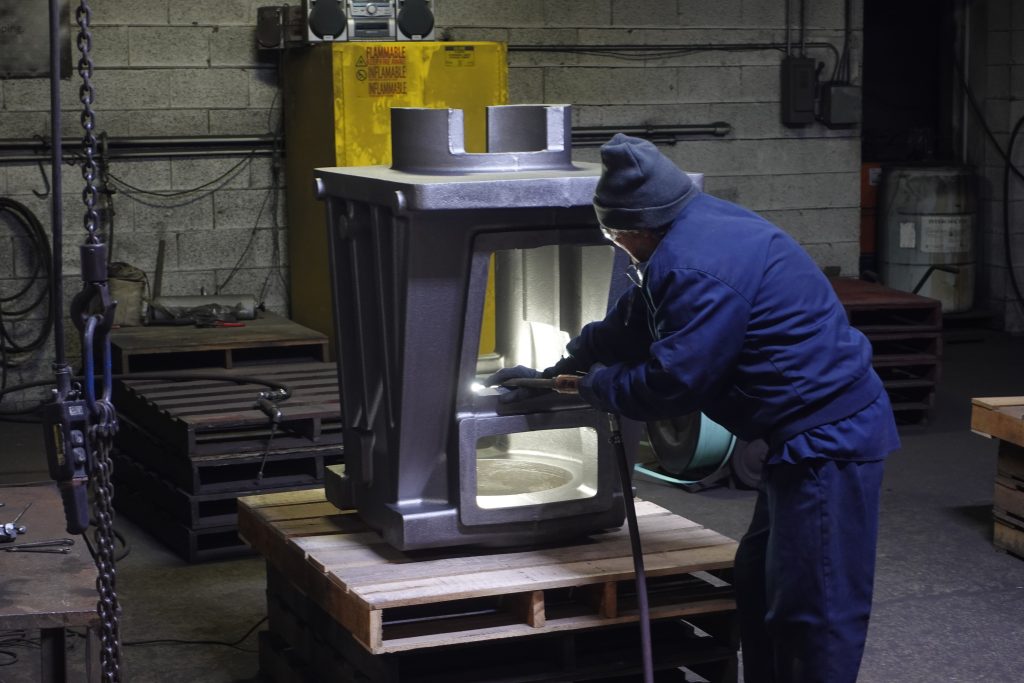
What PMC offers current and potential customers
The commitment to remain an industry leader in quality means PMC has several programs and value-added services that can help save customers time and money.
PMC offers a limited inventory program. “We will deal with stock supply if it’s a customer that orders on a regular basis,” said Permenter. “If they consistently give us the same purchase order for the same part over and over again, we know we can produce that ahead of time and keep an extra two to five pieces.” Permenter says due to the size of PMC and where it’s located, they really can’t allocate more room than two to five pieces.
Another way PMC makes life easier for customers is our impressive on-time deliver rate. We deliver 95% of our orders on time. We have production lead times of a remarkable 3-6 weeks, meaning we can take your order and get it to you very quickly.
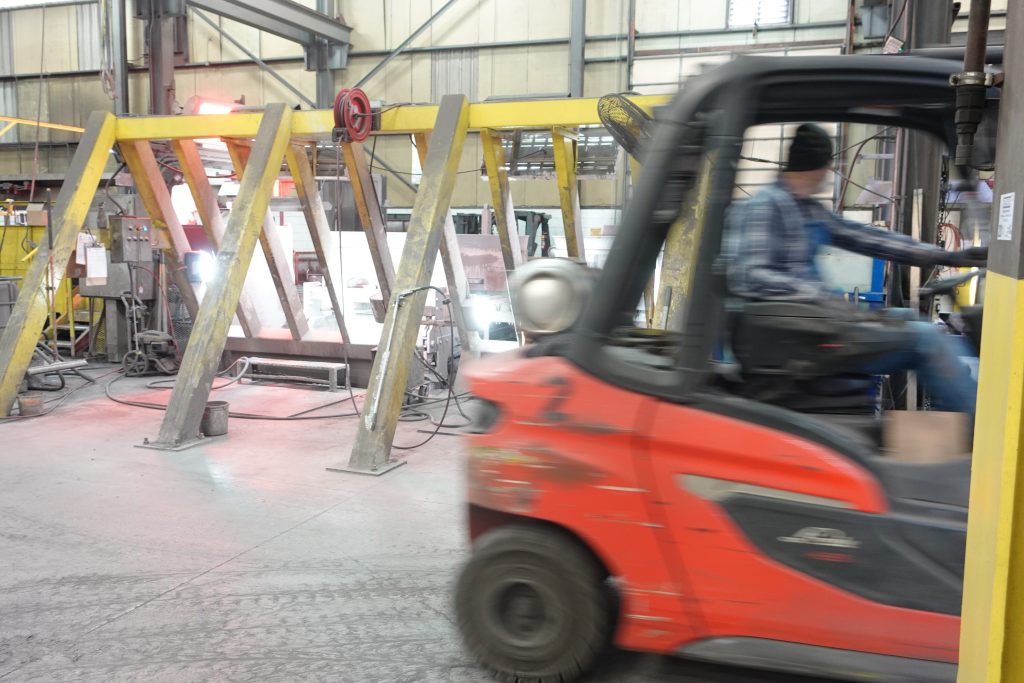
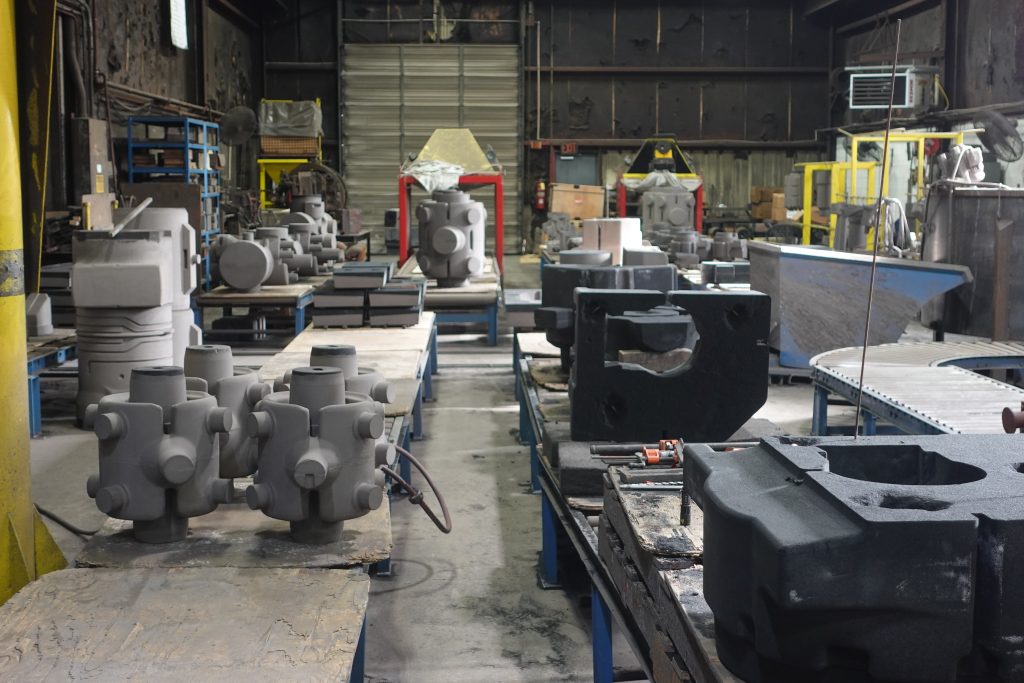
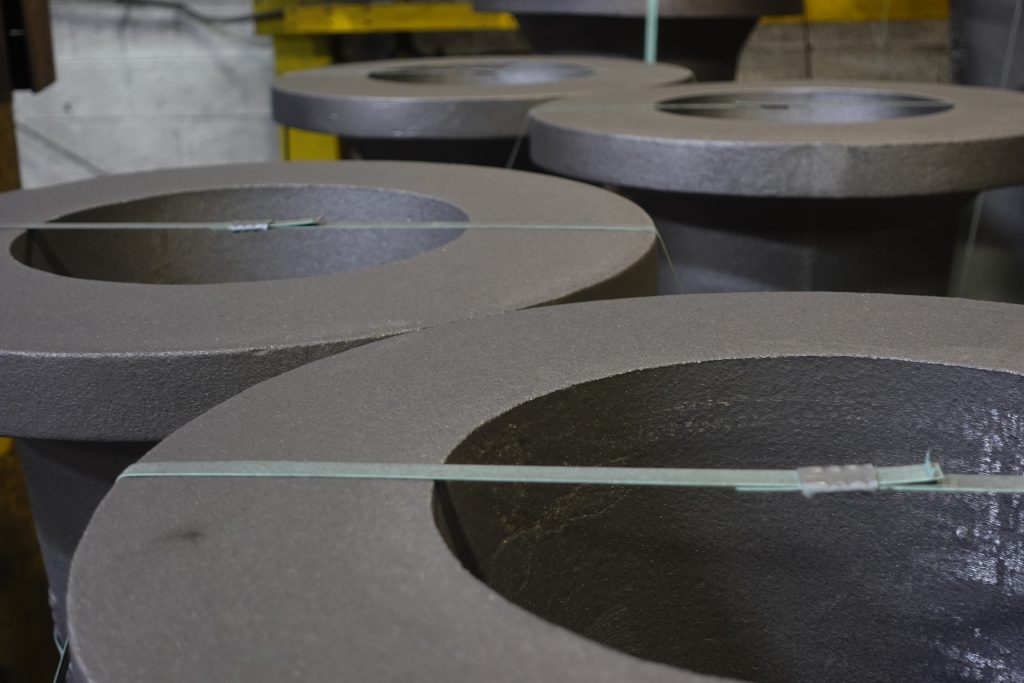
Certifications for business management and safety
Penn-Mar Castings has a long list of certifications, guaranteeing that we follow the best guidelines for business, efficiency, quality and safety.
PMC is Lloyd’s register certified. Lloyd’s is a leading provider of classification and compliance services, helping clients design, construct and operate their assets safely and in line with environmental expectations.
To go along with that, PMC is also Bureau Veritas certified. This certification comes from internationally recognized management standards. It provides certification and training services to help reduce risk, inspire confidence and continuously improve.
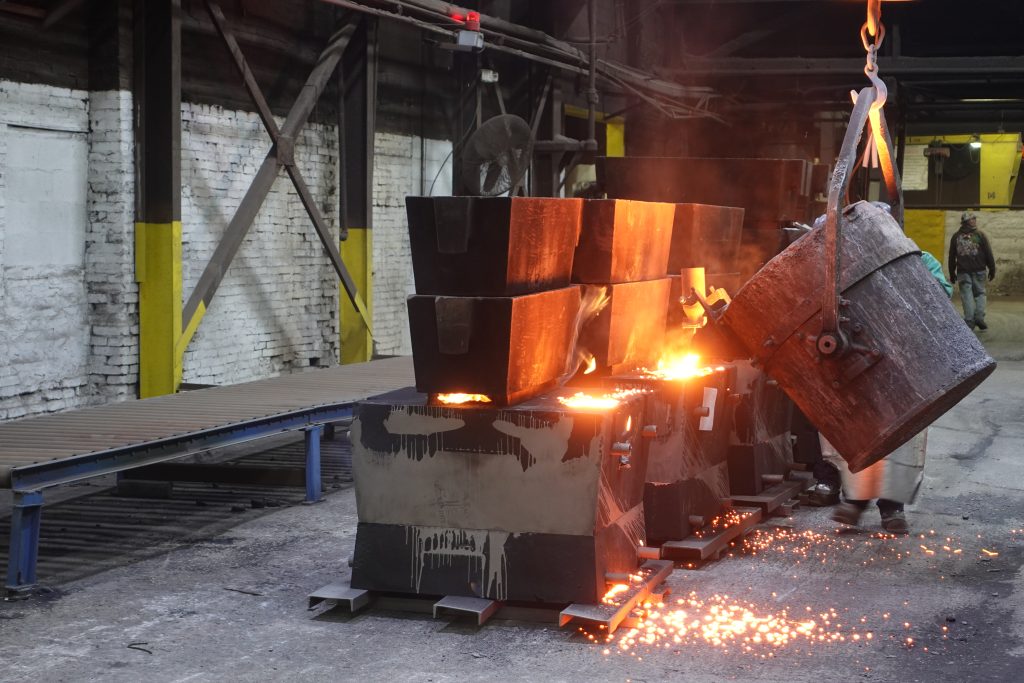
We are also both ISO 9001 and 14001 certified. ISO 9001 assures organizations are meeting customer and regulatory requirements and they are improving processes and services.
ISO 14001 is for environmental management systems, helping organizations minimize ecological impact, comply with regulators and achieve sustainability goals. “Penn-Mar is located right in the middle of town,” said Permenter, “so we have to really be aware of our safety and environmental impact at all times.”
Permenter went on to say “we are a very clean foundry, we make sure everything stays in the building.” PMC has monthly safety meetings, as well as daily safety audits. Management is always in full communication with every department to make sure everyone is up-to-date with all regulations and requirements when it comes to safety.
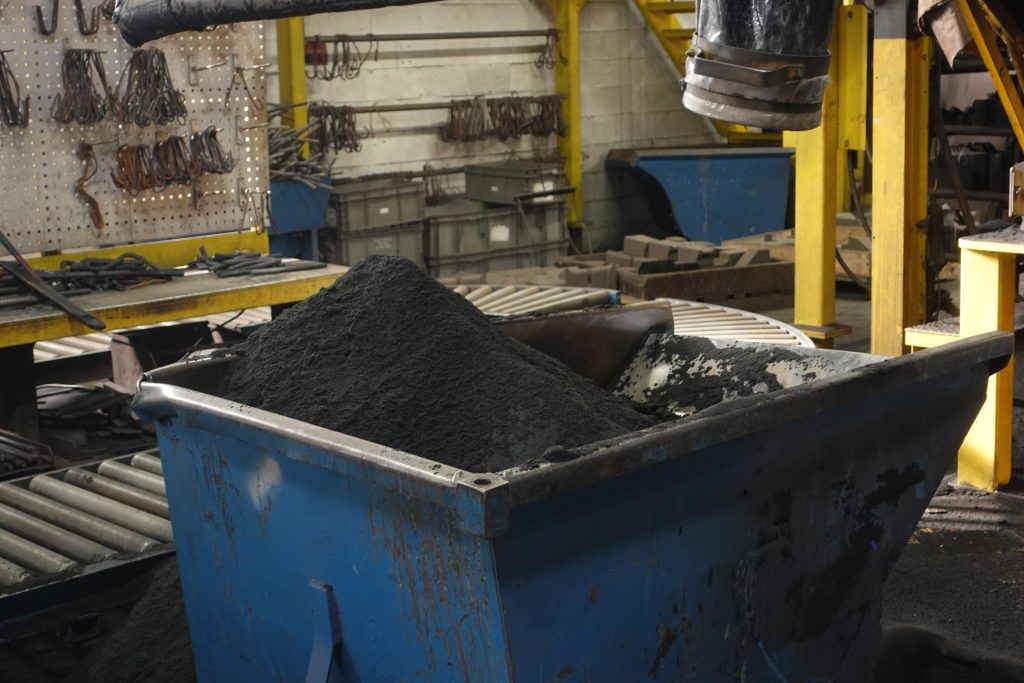
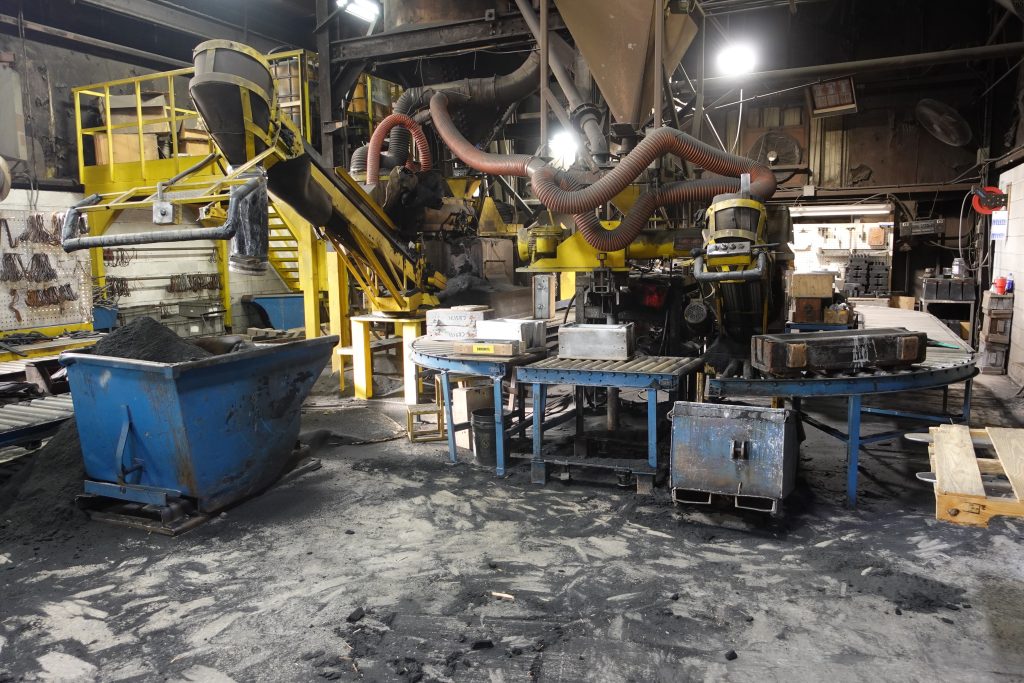
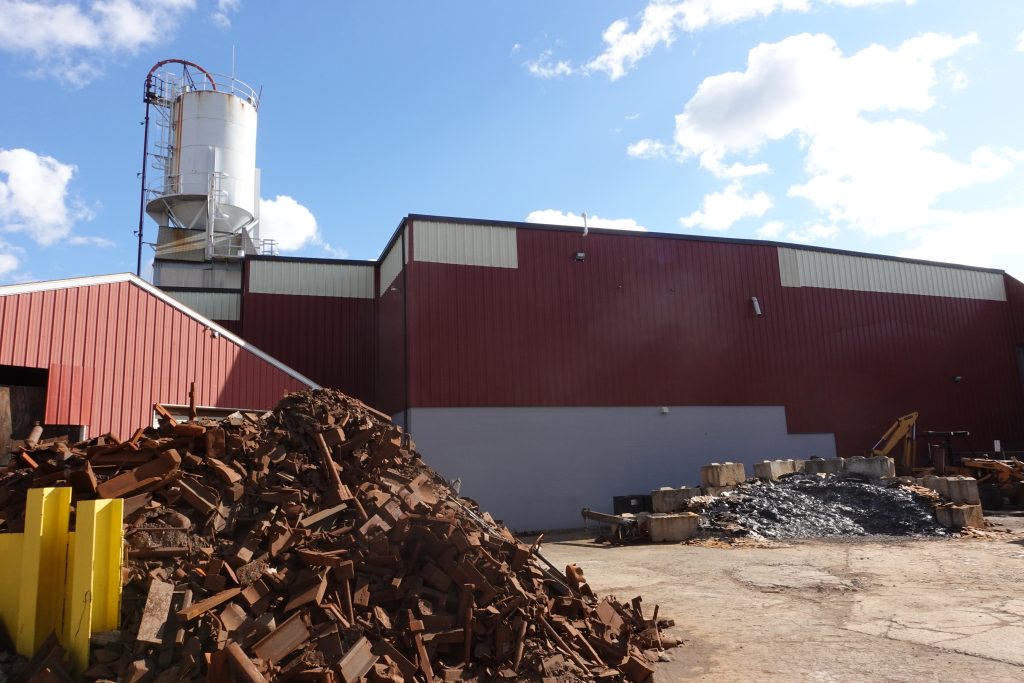
There is a lot of reusing and recycling at PMC as well. “We reclaim our sand and reuse it for every single mold out there,” said Permenter. “Also, if we have a damaged casting or castings, we are able to remelt those, depending on the metal itself.”
A culture of inclusion, growth and family
“One of the main reasons I’m here at Penn-Mar is because of the culture,” said Permenter. “We are a family. We get down to business when we need to, handle what needs to be done, but after that we make sure we are all on the same page and we all communicate thoroughly.”
She also pointed to employee morale boosting events that management hosts including cookouts, celebrating the good things happening with workers, rewarding great work with gift cards and honoring people for hard work.
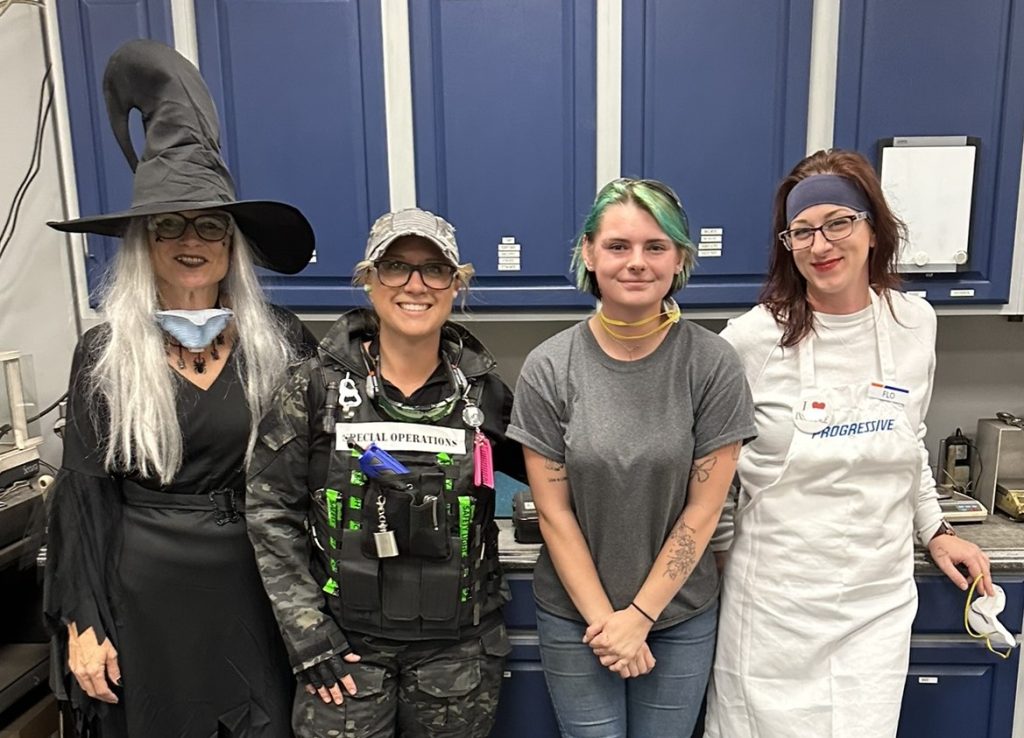
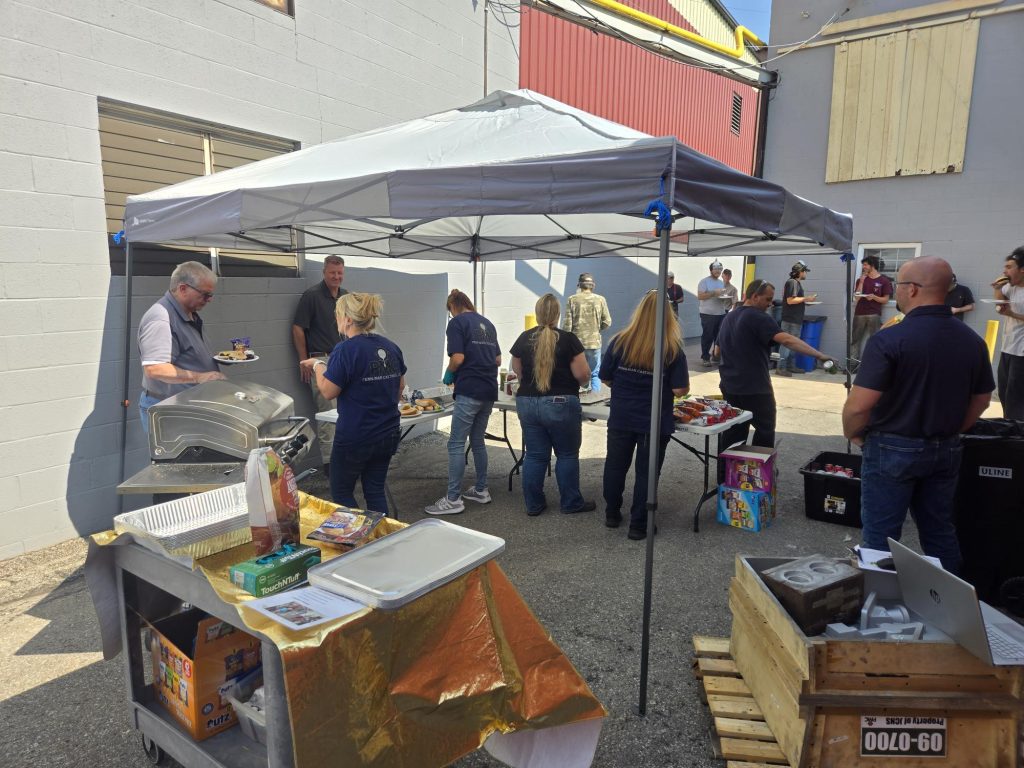
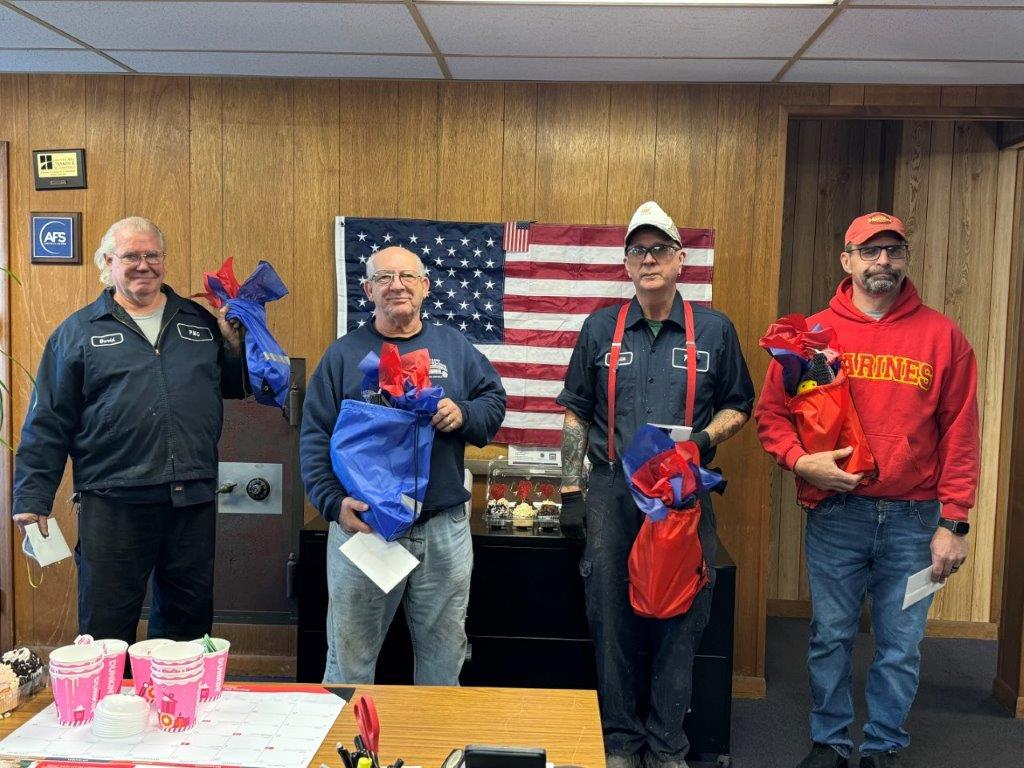
“Someone should work here because of the environment alone,” said Permenter. “We accept all different kinds and we have the individuals grow based on their own needs and skills.” PMC has growth plans, providing employees with the tools and knowledge to learn new skills and new jobs.
“Working here with this team, I have never felt more invited and more welcomed. I have managed to grow just with the knowledge I have, but not only that, I have gained a whole entire new family,” added Permenter.
Learn more about what PMC can do for you
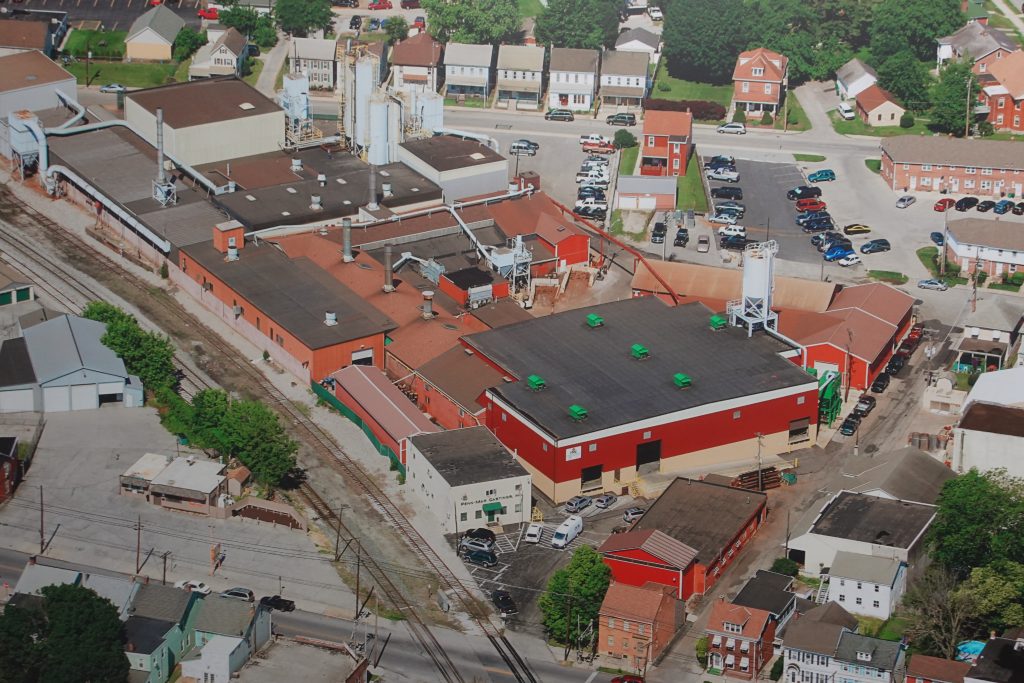
What you’ve just read is only part of what PMC can do and it’s only part of how we are better than the rest. You can see how Penn-Mar Castings stacks up against other foundries by visiting our website here.
PMC manufacturers high-quality, multi-cored, gray and ductile iron castings. They range in size from 5 pounds up to 5,000 pounds. PMC specializes in the 700-1,000 pound casting range.
If you are interested in our high-quality castings, amazing customer service and a remarkable on-time delivery rate, please give our crew a call today at 717-632-4165.