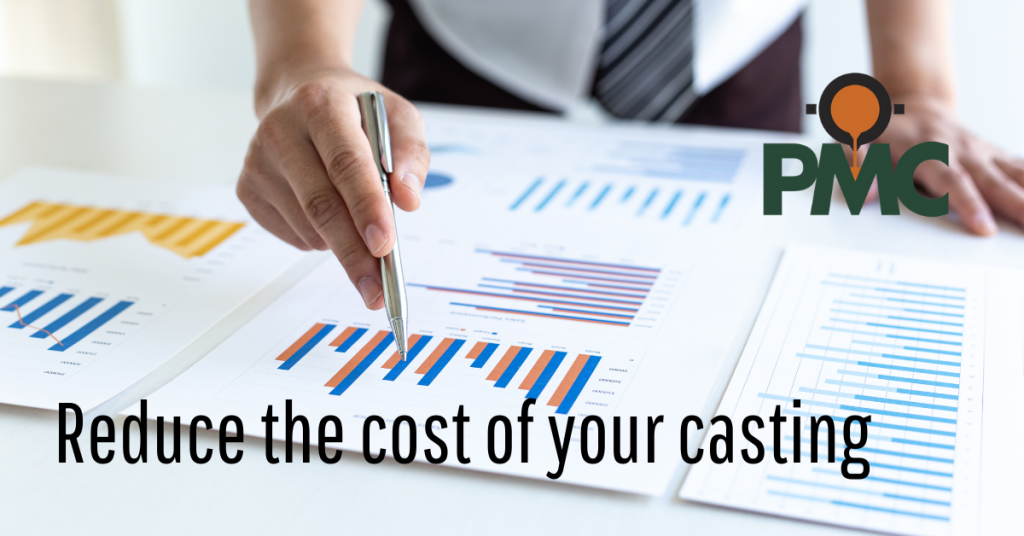
A lack of casting knowledge is at the root of nearly every cost driver for castings. To complicate matters, even if you have general knowledge or experience in casting, every foundry uses different processes. What works to reduce cost in one operation can drive up the cost in another.
Even if you have general casting knowledge, get the foundry involved as early as possible in the design process. Casting engineers and designers have greater control over the cost of a casting than you might expect. Here are some major cost drivers and what you can do from the engineering and design perspectives to optimize your investment.
Understand the capabilities of your foundry’s process
If you need several castings that range from 50 lbs. to 5,000 lbs. for a project, they may not be designed the same way. Large foundries often need to do multiple cavity tooling to reduce the cost of smaller parts. They also require different configurations and setups than the larger castings.
Improper casting design
Improper design, such as defining parting surfaces, planes, and draft, can quickly hinder the foundry from leveraging the design to produce it cost-effectively. Get your foundry involved early on to solve these issues, long before the castings reach the foundry floor.
Tolerances
A common cost challenge occurs when design engineers call for overly tight tolerances where they are not needed to provide fit, form, and function. Global Dimensions and Tolerances (GD&T) are a system for defining and communicating engineering tolerances by using symbolic language on engineering drawings (click here to view an article by our sister company that provides a more in-depth discussion of GD&T). It explicitly describes the part geometry and its allowable variations. If a design engineer uses it without fully understanding its principles and best practices, it can complicate the part and mold design process (increasing cost).
Complexity
Some parts require extensive cores or, in some cases, even specialty or 3D printed cores, which are very expensive. In general, the more cores a part requires, the higher the cost.
Quality requirements
An excessive quality requirement can drive up part costs. Examples include:
- Full layouts and scans of every part,
- Drawings that declare that every dimension is critical
- All parts need part-specific chemical and mechanical testing
Tooling design
If patterns already exist and are being transferred to a new foundry operation, this can impact your casting cost. Existing tools that are transferred need to be repaired, modified, or reinforced to work within our foundry processes.
Every foundry is different when it comes to the metal casting process. What works great in one foundry may not work in another. So be sure you get your foundry involved as early as possible in the casting design process.
Contact PMC today to see how we can help you design and create cost-effective castings.